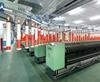
Being the leading brand of short fibre production technologies, Rieter continues standing out with the innovations it offers in all spinning processes as well as its solutions for the textile sector. Ensuring that necessary preparations are made for high quality yarn production, Rieter’s new generation roving frames can manufacture rovings that have high quality continuity with low cost owing to its new drive system and individual roving monitoring system.
Cost-Effective Production
The F 16 roving frame with doffing aid and the F 36 with automatic doffing ensure that the power provided is transmitted throughout the machine at the optimal level owing to its double bobbin drive mechanism. Thus, it saves a significant amount of energy since the power required for the power is minimised. Since direct drive of the bobbins through tooth belts reduces friction losses and improves energy balance, quality assurance and economic production are ensured owing to the drive mechanism developed in F 16 and F 36 roving frames.
Since faultless wind-off of the bobbins leads to fewer breaks, in F 16 and F 36, ROJ roving tension control unit stables the roving tension while obtaining the bobbin. Since no fluctuation occurs in the tension, if there is a break, the roving frame can continue operating without cease. Therefore, high roving smoothness can be ensured at different bobbins and in each bobbin layer.
Energy and Time Saving
Since each and every roving in F 16 and F 36 roving frames can be separately monitored with the removal of extraction, the machine sustains reliability even at the roving breaks. With the deactivation of the extraction system, the installed power is reduced by 4kW and an energy saving up to 3 kW is possible. Since the individual roving monitoring system is connected to a central analysis unit in the machine control system, in F 16 and F 36, the yarns that do not operate can be viewed through the screen and thus, a quick intervention into the problematic bobbins is possible.
Easy Doffing
With the developed doffing concept, the doffing process lasts for less than 3 minutes in F 36 and thus, machine efficiency is maintained even with the thick rovings and at the frequent doffing situations. Since all full bobbins are removed from the spinning area, doffing can take place in a 50 % shorter time when compared to the other systems. F 36 which starts operating the moment when full bobbins are removed and empty ones are inserted also saves time.
The most important advantage of the manual doffing concept of F 16 with doffing aid is that bobbin bank bends forward during the doffing of the bobbin bank, which makes it possible to reach the bobbins located in the front and back. While bobbin quality is preserved in F 16 in which full bobbins can be easily taken, no wind-off problem is experienced in the ring yarn machine. Likewise empty bobbins can be positioned in the bobbin supply box in the operating state, which makes doffing process faster.
The display screen found on both machines enables the machines to be easily adjusted to all kinds of raw materials and facilitates detailed adjustments for the graphical display of different processes either at the first operation or lot change. In F 16 and F 36 where data can be stored for 50 different lots in the control system, different compositions are easily accessible.