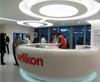
Taking place among the biggest textile machinery producers, Oerlikon showed off in ITMA Asia fair. The company, exhibiting its products in an 1200 squaremeters area, focused on Autocoro 8 rotor machine, new solutions on ring yarn and spinning systems, WINGS – the FDY spinning machine, twisting and embroidery solutions. Apart from these, Oerlikon made visitors watch complex set up treatments and process steps of nonwoven, man-made staple fiber and and BCF carpet yarn businesses on ‘virtual showroom’ in 3D.
In Oerlikon Group organization, innovative industrial solutions and advanced nano technologies on textile machines, drive systems, vacuum, thin plate coating and are produced. The firm is based in Switzerland, having a past of more than 100 years, and produces service in 38 countries, more than 150 regions, with its nearly 17000 employees. Having acquired 3, 6 billion CHF turnover in 2010, this global firm made 239 million CHF investment in the same year, having more than 1200 AR-GE specialists within. The group, one of the producers that predominate in the global market, took place with its most exclusive products in ITMA Asia. Some of these products are as follows;
Special Solution to FDY Yarns from Barmag
Oerlikon Barmag presented its solutions that provide efficiency increase, energy saving, ergonomic use to the Chinese producers. While focus point of the firm is WINGS machines for FDY yarns, it also spared a place for the spinning systems necessary for WINGS and FDY systems. Other machine presentation of the firm,Win Trax was also appreciated by the visitors. Carbon fibers, used as complementary fiber in composite materials, are regarded as materials of the future. In this context, Oerlikon Barmag, which continues producing new technologies, succeeded to receive compliment with the machine that brings solutions to the manufacturing of fibers, whch is, indeed, very hard to do. Oerlikon Barmag, receiving interest due to its 12 yarn WINGS machine for Polyamid 6, market leader of filament facilities, presented practical solutions in texturizing and spinning high-end filaments to yarn producers in the fair. It is also stated that WINGS sets new standards for transforming polymer, which is hard to process, to good quality yarn.
Innovations from Oerlikon Schlafhorst in Yarn Spinning and Rewinding
Oerlikon Schlafhorst, strong market player in ring and rotor spinning and winding supplies continues to offer spinning mills worldwide with innovations for the optimum in quality, reliability and economic benefit. The new Autocoro 8 is thus the first and only rotor spinning machine to spin a yarn at a rotor speed of 200,000 rpm. The new technology forms the basis for productivity increases of up to 25 percent, machine start-up in minutes instead of hours, an excellent multi-lot capability and much lower spinning costs. The brand also presents the longest semi-automatic rotor spinning machine in the world with BD 448.
The new Zinser ring spinning machineZinserImpact71 promise unique process reliability with the Impact FX compact spinning technology. And the quality package of the Autoconer X5 sets the benchmark for individually and flexibly adaptable package quality with maximum productivity.
Oerlikon Neumag: Leader Force for BCF Carpet Yarns
With a market share of 70 percent, the company is a leading supplier of highly advanced BCF carpet yarn machines and it is another important brand of the fair. The best seller three ends machine in 2011, the S+ is now available for production of the favourite carpet material polyester BCF.and the BCF S+ for polyester is a perfect substitute for polyester spun yarn on account of its cost efficiency in production. While the production facilities for polyester staple fibres permit maximum capacities of up to 300 tonnes per day, it reduces operating costs at the same time. For manufacturers of nonwovens such as geotextiles, compact inline facilities with capacities of up to 80 tonnes per day offer suitable solutions as they permit small production batches and require few operators. Also on the agenda are machines or turnkey systems for the production of nonwovens from spunbond and meltblown to airlaid.
Up to 50 percent Energy Saving from Oerlikon Saurer
Developing technologies for knitting and twisting industries, Oerlikon Saurer announced that it created an energical difference with Volkmann CT. Eco-drive concept and spindles are the perfect complements to the e-save spindle family and help to save up to 40 per cent of energy costs, even for the finest yarn counts. Other innovation of Saurer, Volkmann Heat-SET integrates cabling, thermofixing and winding in one process sequence, thus reducing process costs and speeding up order completion. The new Allma TC2 two-for-one twisting machine can process every conceivable material in the titre range from 235 to 60,000 dtex. It thus satisfies the demand for top quality, application variety and production flexibility in the market for technical plied yarns. Allma CC4 is revolutionizing the tyre cord cabling market with energy savings of up to 50 percent. And the Epoca 6 with its new drive system, optimal adjustment options and perfect thread cutting delivers the product up to 30 per cent faster with maximum reliability and embroidery quality.
Oerlikon Textile Components: Address of Quality
Oerlikon Textile Components, market leader in terms of quality and know-how in the production of premium components for the filament industry and staple fibre spinning mills, exhibited the innovations it demonstrated in ITMA Barcelona also in ITMA ASIA. In staple fibre spinning, the world’s most versatile Texparts® PK 2630 SE weighting arms products can also be used in Rieter and LMF machines. Spindles with the Texparts® Zero Underwinding system prevent underwind threads and offer maximum reliability, efficiency and operator-friendliness in use. The novel curved edge of the Daytex® Shrinkage Belt is completely devoid of sharp edges,preventing tears from forming and thus extending the belt’s service life. Accotex, Fibrevision, Heberlein and Temco, the product series that have already proved themselves, have an important place within the industry as the complementary products of these series.
New Production Facility in Asia will be Turning Point
Swiss multi-national textile machinery producer Oerlikon announced the official opening of its new headquarters in 19th June in Shanghai. While the firm has eight sales and service offices currently in operation in Shanghai, it aims at uniting all five business Segments under one roof.
Oerlikon’s global CEO, Michael Buscher, made important explanations with regards to the subject, saying; “China has become Oerlikon’s most important market. The opening of our new Chinese headquarters is remarkable as it is one of the most important indicators of our expanding strategy here. Emphasizing that the new headquarters to be a turning point, Buscher continued; “This enterprise is a step promoting further growth in Asian Region or China. We continue our investment in China and we have demonstrated this through our investment of more than CHF 38 million Swiss franks in China over the last three years”.
According to the statement made by the firm, the production facility in Suzhou is the largest facility of the company in global terms. The firm, with this global Asian headquarter, aims at exercising control over the whole Asia Region. In the statement of Clement Woon, a Singapore native and new Oerlikon Textile CEO, it is informed that 40 percent of textile’s senior management will be based in here.
In 2011, China, heading Oerlikon’ s growing markets, constituted 28 % of total sales in China, a growth rate of 32 % compared to 2010 and 138 % compared to 2009. In 2011, Asia overall was responsible for 49 % of Oerlikon’s total sales. In 2012, it increased at a rate of 22 % compared to 2011.
Oerlikon has a long history in China. Oerlikon Textile has been actively operating in China since the 1960s. The firm, wishing to reinforce its status with long term investments in the region, comes forth with the production, sales and marketing facilities it established in China. Launching Suzhou production site in 2005, Oerlikon opened two new coating centers in Jinan and Chongqing in 2011. Oerlikon, as it stands today, has 9 sites in China and employs approximately 2 500 Chinese people.