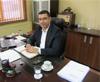
Biska, established by Kaplan Family, entered the sector in 1972. The company started the production firstly in its cotton gin factory in Gaziantep, focused on production after having been institutionalized with 28,800 spindles in 1999 by Burhan Kaplan under the name Biska Tekstil Sanayi ve Ticaret A.Ş. Biska Teksil, which has left 30 years behind, reached 62,400 spindles with the investment of a new compact facility in 2010. The company is able to perform production between Ne 30 and Ne 40 tons per day. Biska, which performs production in its facility in Gaziantep for the domestic market and exports, highlights quality in yarn production with its staff of 250 people.
Biska, which is one of the leading yarn manufacturers of the region, produces combed, carded, combed compact yarn, flamed yarn, lycra yarn types between Ne8 and Ne 80. The products of the company, which has a broad production scala, are used in the knitting and weaving sectors.
Biska, which includes the machines of well established foreign companies in its machinery park, prefers Trützchler in blowroom and carding machines. The company operates with 4 foreign fiber and PP seperator in this group and prepares for the production process with 44 carding machines. The drawframe, comber group of Biska includes Rieter and Trützschler drawframes, 3 lap machines and 28 combing machines. In the bobbin group, there are 20 Ling Schlafhorst and 20 Link Murata 21 C machines whereas the roving and ring group incudes 13 Zinser RM670 automatic transprotation system roving frames, Zinser RM350-351 with a spindle capacity of 28.800 and Zinser 351 compact machines with a spindle capacity of 33.600.
Ramazan Kaplan, Vice Chairman of Biska Tekstil, which continues to increase its production capacity and export power with its quality and technological machinery park, gave important information about the company. Kaplan emphasized that the cotton production machines should be prepared at the end of the processes requiring experience. “Therefore we work with the companies, which carry out healthy R&D activities so we establish our machinery park with the machines of the foreign and well established companies,” said Kaplan and reminded that all the machinery manufacturers working in the field of short staple manufacturing, are in the foreign countries. “Almost 100 percent of the sector establishes its machinery park by importing machines from the foreign countries. The production of short staple fiber machines focuses on R&D and requires too much experience and money. Therefore we prefer in our investments the machines of the well established companies using the latest technology,” said Kaplan.
Kaplan gave information also about meeting the need for raw materials and said that they supply raw materials from İzmir, Diyarbakır, Şanlıurfa. He remarked that they prefer America and Greece for the raw materials to be used in the exports.
The Government should Continue to Provide Incentives
Kaplan reminded that Turkey experienced crises from time to time. “The cotton yarn sector was severely affacted by the low exchange rates and the economic crisis prevailed in 2007-2008,” said Kaplan and added that during this period, many well-established companies were closed down or suspended production. “The textile country Turkey, turned out to be a country that imported textile,” said Kaplan.
Kaplan stated that with the customs duty applied on the imported yarn, the sector started to recover. “The recovering sector brought about new investments. During 2010-2011, many investments were made and the production and demand increased within the yarn sector. In order to maintain this atmosphere in the sector, all the players within the production process should do their part. Besides, for the development of the yarn sector, the government should continue to provide incentives and the taxes on the imported yarn and fabrics should be long lasting,” said Kaplan.
Biska Operated at Full Capacity in 2011
Kaplan, who underlined that the additional taxes applied on the imported fabrics in 2011, affected the yarn sector in the good way, remarked that the unemployment rates declined and the yarn manufacturers started to operate at full capacity in this period.
Kaplan stated that 2011 can be considered as a successful year for them too. “We operated at full capacity and allocated 75 percent of our production for the knit and apparel manufacturers engaged mostly in exports and 25 percent for the companies in the European countries,” said Kaplan and emphasized that they will continue to operate at full capacity also in 2012 and that they expect new demands to occur in the sector in parallel with the customers’ demands.