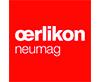
The Chinese carpet yarn manufacturer Zhejiang Sitong New Material Technology Co., Ltd. is expanding its polyester capacities with the commissioning of an Oerlikon Neumag BCF system of the BCF S+ type. This will enable the company to ensure a balanced production of polyester, polyamide and polypropylene yarns.
With a total capacity of 50,000 tons per year, Sitong is one of the largest BCF yarn manufacturers in Asia. With the additional four BCF S+ positions for polyester yarn, the company from Hangzhou is responding to the trend towards polyester carpet yarns. In the future, Sitong will use them to produce balanced BCF yarns made of polyester, polyamide 6 and polypropylene. “Our strategy is a broad portfolio; this makes us more robust in the face of trends and market fluctuations” says Tang Liang, President and Owner of Sitong. The decision in favor of Neumag was based on the good experiences. “Since our foundation in 2002, we have relied on technology from Europe; for polyester production, we only consider Oerlikon Neumag plants. We have established ourselves with our quality products in both the local and international markets; this shows that we have made the right investment decisions.”
BCF S+ is Flexible
The new BCF S+ Monocolor plant is designed for polyester yarn production, but it also produced excellent data during the production of polyamide 6 yarn during the commissioning process. The ability to quickly switch to the cost-effective production of high-quality PA6 yarn gives Sitong a significant competitive advantage. “Trends are becoming increasingly short-lived. However, investing in a plant is a long-term decision. So it's a strong argument if I can spin different polymers with the same system without sacrificing the quality of the end product” Tang Liang sums up.
Carpet Market in Asia is Gaining in Importance
The Asian carpet market is currently experiencing noticeable growth. While the focus of carpet yarn production has been in the US and Turkey so far, Chinese BCF yarn production in particular is experiencing a real boom in the post-corona years. This is due, on the one hand, to the strengthening of the Chinese automotive sector and, on the other, to the resurgence in travel. “Many hotels are currently being renovated and new ones are being built. During the pandemic, many hotels were closed, but now there is a significant backlog demand” says Sun Peng, Sales Director at Oerlikon Neumag in China, assessing the increased demand.
About Oerlikon Polymer Processing Solutions Division
Oerlikon is a leading provider of comprehensive polymer processing plant solutions and high-precision flow control component equipment. The division provides polycondensation and extrusion lines, manmade fiber filament spinning solutions, texturing machines, BCF and staple fiber lines as well as nonwoven production systems. It also develops and produces advanced and innovative hot runner systems and multi-cavity solutions for the injection molding industry. Its hot runner solutions serve business sectors, including automotive, logistics, environmental, industrial applications, consumer goods, beauty and personal care and medical. Moreover, Oerlikon offers customized gear metering pumps for the textile, automotive, chemical, dyes and lacquers industries. Its engineering competence leads to sus-tainable and energy-efficient solutions for the entire polymer processing value chain with a circular economy approach. Oerlikon Polymer Processing Solutions Division serves customers through its technology brands – Oerlikon Barmag, Oerlikon Neumag, Oerlikon Nonwoven and Oerlikon HRSflow – in around 120 countries with production, sales, distribution and service organizations. The division is part of the publicly listed Oerlikon Group, headquartered in Switzerland, which has more than 12 600 employees and generated sales of CHF 2.7 billion in 2023.