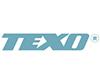
“Rather surprisingly, given that China is now by far our biggest single market and the paper manufacturing industry has been gradually consolidating in Asia, we currently have new orders from both long-established North American and European customers,” says , TMAS member Texo AB President Anders Svensson. “The current global political tensions in combination with insourcing to Europe and North America have been important factors for these projects and I’m sure the evironmental benefit of significantly reducing transportation played a part too.”
Application Stages
Principal products in the PMC segment include forming, pressing and dryer fabrics, all of which convert the initially wet mass of fibres through the paper machine as water is progressively squeezed out of it, ensuring it is held in place and air can be effectively blown through it at the dryer stage, to ensure a regular shape and extremely even surfaces.
PMC products can be up to 140 metres long and in the past have been made in extremely wide widths – the largest weaving loom manufactured by Texo had a working width of 31 metres.
TCR Weaving Looms
The company’s TCR loom has been specifically developed for the production of very fine and tough forming fabrics where the highest quality is critical.
The FSX model is designed for the production of both forming fabrics based on medium-to-coarse yarns as well as press felt base fabrics, while the TMR is an extra heavy high-speed loom developed for both forming and dryer fabrics, as well as industrial fabrics such as filter materials employed in applications such as dewatering in the mining industry.
All of these looms are characterised by advanced features based on Texo’s over 60 years of know-how and constant development, including the company’s proven Pozi Grip rapier insertion system, Disco dobby unit, LoCoMo control system and TDD direct drive.
“At ITMA We Emphasized The Fact That We Have All Alternatives Available”
At ITMA 2019, however, Texo showcased a section of one of its latest models with a more traditional cam drive, for which there is still market demand. “We introduced the first weaving loom with an electronic drive for this industry over a decade ago and it’s been very successful, but there are still some companies who want to go the traditional way,” Svensson explains. “At ITMA we emphasized the fact that we have all alternatives available.”
TMAS companies will have a significant presence at the Barcelona show, where their emphasis will be on the latest automation concepts and the use of advanced sensor systems for enhanced and more resource-efficient manufacturing, according to TMAS Secretary General Therese Premler-Andersson. “It’s ironic that while TMAS member companies are very much involved in accelerating Industry 4.0 concepts, their technologies continue to be crucial across many traditional industries such as paper making, where the use of technical textiles is perhaps not so widely appreciated,” she observes. “This is just one example of the huge and sometimes unexpected number of end-use markets served by our members as they have diversified from conventional textile technologies over many years.”