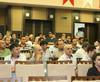
Serving the textile sector with the slogan of market-oriented solutions, Suessen introduced its latest innovations to the firms operating in the region with an organisation held in Kahramanmaraş. Since its establishment in 1920, Suessen has had an important position in the textile sector with its innovative approach to the spinning processes, in particular. Suessen shared the latest developments in the yarn industry with the participants in the seminar it organized.
Having great breakthroughs in the sector with SE Spinning Boxes for Autocoro Open End (Rotor) Yarn Machines SE 7 – SE 10, HP-A and HP-GX drafting systems for flyer and ring yarn machines and of course EliTe®Compact Spinning System since its establishment, Suessen is among the firms leading the sector in terms of compact systems and open-end yarn machines.
EliTe®Compact System
Accelerating its promotion activities with the events organized before ShanghaiTex 2015, one of the important fairs of the textile sector, Suessen inserted the absorption tubes on the ring spinning machine in Elivac CDS Central Vacuum System found in EliTe®CompactSet which is the most popular system of the sector in the field of short fibre and worsted ring yarn. The advantages of this system include easy and fast installation, lack of individual ventilator system for EliTüp absorption tubes, absence of frame-belt-roller and rotating drive mills, less energy consumption up to 20 %, less need for maintenance and less need for spare parts.
Open-End Rotor Spinning
Offering Premium Parts Modernisation for open-end rotor spinning machines, Suessen has designed SC2 and SQ2 Spinning Boxes especially for the spinning of synthetic fibres and ensured production increase up to 40 % and significant decreases in yarn breaks. Thanks to the system with a rotor speed exceeding 135 thousand, an output speed of 220 meters per minute can be achieved.
ProFiL®Cartridge
With ProFiL®Cartridge, the rotor bedding system which does not have oil emission, Suessen removes the disadvantage of oil emission into the spinning box and prevents rotor blockages resulting from oily flies. In this way, significant reductions are achieved in the maintenance costs. With ProFiL®Cartridge where oil change is not necessary in the thrust bearing, stable drive moment is created depending on the movement of the clean feeding mill and right axial rotor support is ensured via steel ball.