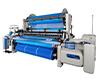
Turkish textiles intense interest in Picanol products was outrageous at the Product Launch Event that was chaired by Picanol Sales Manager Vincent Geldhof and Picanol Turkey Denizli Uşak Regional Sales Manager Derya Sargın.
Weaving the best quality terry you can imagine. Ready for all challenges whether it concerns low-pile, high-pile, like fabrics or bath-mats whether you’re weaving simple border or complex and fancy border where they concentrate on three pick terry, or make all possible variations with 3-pick, 4-pick, 7-pick or even 12-pick terry. Terry Max-I can handle any design. The basis to realize this is the pile formation system. The pile heights changing device offers you absolute freedom of design. You have the possibility to program whatever pile heights between 0-12mm height and whatever design or pattern. Be its standard terry or weaving patterns, the pile heights can be changed loop by loop but also the individual distance between every assertive pick can be freely programmed.
This is realized by the pile heights water that is directly driving torsion-free shaft driving the cloths and the backrests movements simultaneously. Accurate pile formation is assured over the width of the machine. Being a two meter sixty machine or even a four meter execution, the fabric quality is further ensured by the minimal distance between the cloth formation and the take-up.
The Key Parameter to Determine the Quality of your Terry Cloth
The key parameter to determine the quality of your terry cloth however, is determined by the way you program the tension of the pile warp. We have developed to this extent the pneumatical file backrests. How does it work? It combines on one hand perfect flexibility with on the other hand perfect rigidity. The flexibility is given by the pneumatical spring that is automatically programmed and which compensates depending on the set tension in the ward. Then different tensions are programmed between for instance pile and border weaving; the compensation of this carbon tube that is very rigid and very light is automatically and immediately adapted. Guaranteeing perfect transition between pile or border or vice-versa. It also means that the pile can be woven with nearly zero tension; on top of this for people who don’t want to do periodical weight control; we have the pile monitoring device that allows you to exactly measure the amount of pile that is given to the towel.
If it exceeds certain ranges, you can ignite warning them or it can even stop the machine if deviation is too big. It guarantees you a perfect and exact weight of your towel.
If the pile formation system is the heart of the machine, then the blue-box, control-box is definitely the brains of the machines. Right from the start, the blue-box electronic platform was designed to meet the needs of next generation weavers.
Ready for Industry 4.0
We developed it for Omni-Plus Summum and in the meantime it has been produced for about 40 thousand times, and is operating all over the world and satisfies customers. High reliability, development, in house, and also produced in-house, It has a processor with an extremely high-speeds that does not only process data in real time but it also has a big storage capacity where we can store data that can be transmitted easily later on for the processing; for example in case of troubleshooting, or for further productivity optimization. The connection or the communication with the machine goes through our newly designed blue touch interface. The new display was introduced on our machines during the ITMA 2019.
First of all, the size increased dramatically, compared to the previous generation. 15.6 inch to be exact. Moreover, it also equipped all functionalities you know from your smartphone. You can touch but you can also swipe from one screen to the other, so that the ease of its use of it, really interactive control specifically for the terry machine we have introduced a couple of dedicated screens that makes the life of the terry weaver considerably easier.
Another novelty is the integration of the machine manual in the display. Next to this, the new platform has been equipped with all modern communication technologies. There is of course Wi-Fi, there is Bluetooth and there is also near field communication. Talking about setting and digitization, Picanol also introduces different features, the distal settings, the replacing mechanical settings, and making the machine driven by data. It enables the user to faster get optimum settings and performance of the machine. This also makes the settings re-producible and easy to copy to other machine.
Thanks to its Independent Drive, the Cutting Moment can be Controlled Individually
A third example of the move to digitalization is the tets or tension display which records the distance between the s-flex and the pre-winder drum and visualized it on a small display. The tets you can quickly manage possible settings differences between pre-winder. This machine is equipped with mechanical filling cutter but it can also be equipped with smartcut for more demanding yarns. The smart-cut filling cutter is another example of a digital setting that at the same time also focuses on sustainability. Thanks to its independent drive, the cutting moment can be controlled individually. As a result, the clamping and the gripper and the length of filling tale can be fully adjusted per channel. This allows every filling combination to be cut and clamped at the exact moment required. Ensuring flawless insertion with a minimum waste. Next to the standard clipper opener, we can also use the air hole that offers an electronic setting of the gripper opening instead of the traditional mechanical opener. The electronic right hand gripper opener system allows to choose the moment of opening the right hand gripper for each individual channel. In this way, the length of the weft tale can be optimized for each filling yarn. With airhole or electronic right gripper opener, it can now integrate sustainability in the design of the machine.
Other novelties are the push buttons, the warning lights and the signal lamp. The push buttons have been changed to membrane technology. Combining durability with the latest safety standards, as it can see the push buttons have been integrated in the press plate for optimum access. There is also a blue lightning that is giving feedback and also confirmation to the push button actions for extra safety. The orange warning lights has also been positioned much more visible for the viewer and we have new led lambs that are much more visible are now also fully digital.
The Most Performing Terry Machine in the Market
In fact, the color programmes can be programmed and customized according to your needs. As Terry Max-I is the proud member of the Optimax-I family, the most performant rapier in the markets, it is of course the most performing terry machine in the market.
An important element in the performance is the sumo drive. Since 1996, Picanol has been equipping nearly all its machines as a standard with the sumo drive. High performance, power fill engine, electronic control, maintenance free and directly driving the machine without intermediate gear or belts. The machine standard comes with opt-speed that lets you program the speed according to the quality of the yarn, or the pattern to be woven. But above all, the basis of the machine consists out of a very robust structure. An immediate advantage of this robust structure of course is the quality of the terry, the more sturdy the structure is, the more stable the production of the terry weaving will be.
-What kind of Rapier set up Picanol does use on Terry Max-I ?
On Terry Max-I, Picanol uses the guided GCv gripper. This gripper insertion is the proven technology of the Optimax-i and is the most versatile gripper heads available in the market. Another advantage of this gripper, is the fact that it is the very compact gripper type. This enables us to weave with a very small shed angle that then again is very favorable for weaving the highest quality of terry fabrics.
-Does Picanol recommend rapier technology for Terry?
By nature, due to the weft properties terry fabrics are ideal to be woven on entrance so for maximum output and speed, we recommend air-jet technology with our Terry Plus-I. This airjet machine is based on the platform of our state of the art and very successful Omniplus-i. However, if you want full flexibility, fancy multi-color border or short-runs then Terry Max-I is the best choice you can make. Picanol is the only weaving machine manufacturer that offers both technologies for terry weaving offering any case the best solution for your specific needs. Terry Max-i and Terry Plus-i or fully complementary. It was a really pleasure to explain you some of the highlights of our machine Terry Max-i. Of course we are looking forward to meeting you to see the machine in life conditions. Because the Terry Max-i has everything in it to continue to grow together.