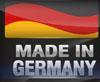
The German machinery manufacturers have the greatest share as the supplier of the Turkish textile sector. In spite of the general decline observed in the machinery sales during the crisis period, the Turkish textile manufacturers didn’t lose their interest in the machines of German brand. The relationship between Turkey and Germany, which is based on centuries traditionally, has a deep rooted history on the commercial and industrial scale. Turkey is also regarded as an indispensable market both in the short and long term, for the German machinery manufacturers. VDMA (Verband Deutscher Maschinen- und Anlagenbau - German Engineering Federation) which includes many German machinery manufacturers that have markets around the world, supports both the promotion of its member companies in the foreign markets and the development of new technologies. VDMA, which has a history of more than 40 years, consists of the companies that develop technologies for the sectors of spinning, nonwovens, weaving, knitting, hosiery and finishing. The federation representing 90 percent of the German manufacturers is at the same time one of the most important textile associations of Europe.
With the technologies they exhibited at their booth at ITMA Barcelona, VDMA and around 130 member companies attracted great interest from the visitors coming from the global market. 83 percent of the representatives of the German companies participating in the fair stated that the fair was pretty good in general and 91 percent of them evaluated it to be a perfect one. Two-thirds of the 134 companies at the fair remarked that they signed sales agreements before the fair ended. In addition to the new technologies of the member companies, VDMA managed to attract attention with the new sustainability project it launched at the fair. BLUecoMPETENCE (Blue-Eco-Competence). In addition to the issue of energy efficiency in the new technologies, other related parameters such as the correct use of raw materials, machines and correct production processes were shared with the visitors at the fair. Brückner, Thies, Oerlikon Tekstil, Dornier, Trützschler, Setex, Textechno Herbert Stein, Karl Mayer and Monforts are the German Textile machinery manufacturers which focused on the issue of efficiency within the frame of Blue-Eco-Competence at ITMA.
The German machinery manufacturers, which achieved a great success at ITMA Barcelona, will display a strong participation in ITMA ASIA CITME, in June 2012, in China. It has been announced that 93 German companies participated in ITMA ASIA in October 2011 and 103 companies took part in ITMA ASIA 2010. It is expected that this figure will be exceeded in 2012.
The Germans are Satisfied with the Export Figures of 2011
According to the final data received from VDMA regarding 2011, in the first three quarters of 2011, the German machinery manufacturers continued to increase their strength. Regarding the export items, spinning machines take the leed with a turnover of EUR 983 million and a share of 47,1 percent. They are followed by knitting and hosiery machines with a share of 29,0 percent and a turnover of EUR 778 million. Later come the finishing, washing, bleaching and dyeing machines with 8,5 percent of share and EUR 516 million of turnover and the weaving machines with a share of 5,6 percent and a turnover of EUR 150 million. According to the increase observed in their exports compared to the previous period, the major markets of the German machinery manufacturers, which gained an income of EUR 2,427 million in the first three quarter of 2011, are as follows; Asia, with 36,2 percent of increase and EUR 1,441 million of income, Europe, with 34,7 percent of increase and EUR 651 million of income, Middle and Central America, with 18,3 percent of increase and EUR 153 million of income, Africa with 13,3 percent of increase and EUR 35 million of income. The only market which experienced a decline in its export revenues is the North American market, which gained an income of EUR 145 million with a decrese of 21,4 percent.
Turkish Market is Distinguished in All Export Items
Considering the 28,5 percent of increase they achieved compared to the first three quarter of 2010, the German textile machinery manufacturers, which increased their exports in all regions except the North America, have shown that they overcame the crisis.
China/Hong Kong, Turkey and India took the third place among the markets, which the German machinery manufacturers perform exports to. In the first three quarter of 2011, 860 million Euros worth of exports were performed to China/Hong Kong. This figure was recorded to be EUR 667 million in 2010. Turkey, which is the second biggest market of the German machinery manufacturers, purchased EUR 145 million worth of machines in 2010 and this figure increased to EUR 217 million in the same period of 2011. The sales performed to India, which is the third biggest market, have increased from EUR 120 million to EUR 201 million. The sales performed to the USA, which amounted to EUR 182 million in 2010, declined to EUR 142 million in 2011. The growth of the German machinery manufacturers in the Latin market continued also in 2011. Brazil, which is the most important manufacturers of the region, purchased EUR 71 million worth of machines form Germany in 2010 and this figure increased to EUR 89 million in 2011.
A couple of slight changes occur in these markets on the basis of export products. In the first quarter of 2011, the spinning machine exports increased by 47,1 percent and China/Hong Kong, which recorded EUR 299 million, became the most important market in this increase. In the same period of 2010, EUR 194 million worth of exports were performed to this market. India, which is the second biggest market for the spinning machines, doubled its imports, which worth EUR 73 million in 2010, and reached EUR 143 million. Turkey, the third biggest market for this item, also doubled its imports and reached EUR 106 million in the first three quarter of 2011. This figure was recorded to be EUR 58 million in 2010.
China/Hong Kong became the most important market also in the weaving machinery sales, which recorded EUR 150 million in total with an increase of 5,6 percent. This market increased its imports, which recorded to be EUR 28 million in the same period of 2010, to EUR 34 million. Iran is the second biggest market of the German machinery manufacturers in weaving machinery. In 2010, the German manufacturers sold EUR 18 million worth of weaving machines to Iran in 2010. In 2011 this figure declined to EUR 14 million. Italy, which is the third biggest market, increased the value of purchase it performed from EUR 11 million to EUR 12 million. When the first three quarters of 2010 and 2011 are compared it is observed that Turkey, which is the fourth biggest market in weaving machinery, experienced no change in the value of purchase it performs, which amounts to EUR 11 million.
Compared to the first three quarter of 2010, the German machinery manufacturers gained an income of EUR 778 million with an increase of 29 percent in the knitting and hosiery machines sales, in same period of 2011. China/Hong Kong obviously had a very big share in this revenue the German manufacturers earned. China increased the import values from EUR 371 million to EUR 458 million. Turkey, which comes after China, increased the value of knitting and hosiery machine imports it makes from Germany from EUR 31 million to EUR 49 million. Turkey is followed by India with EUR 31 million, Taiwan with EUR 22 million, Italy with EUR 21 million and finally by Korea with EUR 20 million.
It is obvious that a serious change has took place in the finishing machinery imports. The USA, which became the largest market with the EUR 85 million worth of exports it performed in 2010, dropped to the third place with EUR 50 million in 2011. Although it decreased from EUR 74 million to EUR 70 million in the finishing machine exports in the first three quarter of 2011, China/Hong Kong became the largest market anyway. Turkey became the second largest market in the field of finishing machines. Turkey, which purchased EUR 46 million worth of finishing machines from Germany in 2010, increased this figure to EUR 51 million in 2011 and became the only country to display an increase among the first three countries. In the finishing machinery exports, Russia took the fourth place with EUR 38 million, Czech Republic became the fifth with EUR 30 million and France took the sixth place with EUR 28 million.
VDMA’s Support Develops the Sector
Thomas Waldmann, Managing Director of Germany’s Textile Machinery Association, made special statements to Textil Dünyası about the works of VDMA and the developments in the Turkish market. Stating that the relationship between the German textile machinery manufacturers and the Turkish textile industry is based on a mutual trust, Waldmann emphasized that the current relationship should be regarded as a partnership. Waldmann remarked that the Turkish textile sector has become more globalized as a result of the successful studies it carried out and that the country is on the way to becoming an important player in the challenging world markets.
Waldmann evaluated the position of the German machinery manufacturers in the Turkish market by saying; “The Turkish sector has a worldwide reputation. Due to the global crisis between 2008-2009, a sharp decline took place in the exports the German machinery manufacturers make to Turkey however the former success in the exports was achieved some time later. Turkey exported EUR 255 million worth of textile machineries in 2008 and this figure declined to EUR 65 million in 2009. The German textile machinery and accessories manufacturers performed EUR 193 million worth of exports to Turkey in 2010. With EUR 217 million worth of exports, this figure was exceeded in the first three quarter, in other words between January-September of 2011. Turkey is one of the countries to send the most visitors to ITMA Barcelona, held in September, in Spain. This is a proof for the development of the Turkish textile sector.”
Waldmann stated that relying on the German technology, Turkish textile sector achieves the best quality, flexibility, efficiency and best value for money. He added that, not only today, efficiency has always been a cornerstone of the German research and technology.
Efficiency Matter Gained Importance in Machinery
Thomas Waldmann stated that efficiency and sustainability in the global markets have become more important than ever before. He added that the high prices for energy and raw materials are worrisome signs for the textile manufacturers. Waldmann stated that VDMA presented its initiative called BLUecoMPETENCE (Blue-Eco-Competence) to the world for the first time at ITMA 2011 Barcelona. “Positioning itself and the technical problem-solvers, BLUecoMPETENCE focuses on saving energy, material and resources regarding the requirements of the society of today and of the future. BLUecoMPETENCE will become an international brand of sustainable technological solutions for the whole industrial spectrum. The campaign started its studies focusing on energy efficiency so The Technology and Research Advisory Board of VDMA has compiled the guide “Conserving resources – secure savings-potential”. For selected process steps used in a textile mill, it describes parameters influencing their energy efficiency and prerequisites for a comparable assessment,” said Waldmann.
“The newly introduced energy efficiency guide of VDMA, aims to help to make the discussion about efficiency criteria, CO2 footprint and comparability discussions more objective,” said Waldmann and added that with in-depth engineering knowledge and well-founded point of view, VDMA carries out its analyses. Waldmann emphasized that it is not easy to define the CO2 footprint of different types of textile machines. “A textile machine is not a consumer product that is designed for standard applications and comparable user requirements. Different types of machines are designed to meed different kind of demands,” said Waldmann. .
Various Parameters Influence the Efficiency
Thomas Waldmann stated that there are a large number of parameters that determine the energy efficiency of a textile machine or a textile process. He argued that the issue of energy efficiency affects how the demand is shaped in the process including the textile manufacturer, fiber supplier and machinery manufacturer. Waldmann remarked that energy efficiency can be defined for each defined parameters and that machines bear responsibility when it comes to carbondioxide footprint. Waldmann continued by saying; “A statement about energy consumption is only significant in relation to the amount of product (kWh/kg product) manufactured. This application is at the same time equivalent to CO2 footprint (CO2/kg product) . A reliable CO2 footprint depends heavily on the operators energy supply.”
Waldmann reminded that the proper use of the machines is very important for ensuring energy efficiency and he argued that energy-efficient machines are a precondition for energy efficiency. Stating that with the proper use of machines, the expected total energy saving is guaranteed, Waldman underlined the relationship between production settings and the energy consumption. Waldmann added that if the investors follow the policy of Life Cycle Cost approach (e.g. VDMA Specificationn 34160) in their investments, they will be able to give right decisions in many cases including the ecological issues.
Waldman reminded that energy efficiency is the focus point in cost savings and that the choice of spare parts and service intervals also influence the energy efficiency. “Lack of maintenance of machines and the use of interior wearing parts reduce the efficiency of the machine and increase the energy consumption,” said Waldmann and added that the machines that meed the demand in energy efficiency can create an added value in the market. Waldmann finished by saying that the BLUecoMPETENCE guide can be obtained in German and in English in the internet via the link www.machines-for-textiles.com/blue-competence.
Blue-Eco-Competence was Launched at ITMA
The BLUecoMPETENCE initiative, led by VDMA, receives a general support from the member companies, which gains an advantage against their competitiors in the global market by focusing on the issues of sustainability and energy efficiency in the machines they developed for the new period.
Roland Hampel, Managing Director of A Monforts Textilmaschinen GmbH & Co KG underlined that with a smart recovery system, energy savings of up to 30 percent can be ensured.
Axel Pieper, Managing Director/CEO, BRÜCKNER Trockentechnik GmbH & Co. KG, said;“The energy efficiency of equipment can only be compared objectively if energy consumption is specifically related to the products. The decisive factor is how much energy per kg of material is used (kWh/kg product).”
Johannes Schmitz, Head of Development, THIES GmbH & Co. KG, stated that high performance and resource protection are indspensable for the entire life of a product. He added that the dyeing lines can be operated efficiently with ultra-short liquor ratios and greatly reduced energy consumption.
Jürgen Meyer, Vice President of Oerlikon Schlafhorst and Oerlikon Textile GmbH &Co. KG R&D made a statement at ITMA and uderlined that sustainability and energy-efficient machines have been the core business of the German textile machinery manufacturers and this face guarantees the economic production.
Peter Schiller, Head of Weaving Machine Technology, Lindauer DORNIER GmbH, remarked that a holistic approach to exploit the full potential for energy efficiency will be their strongest point.
Armin Leder, Director Research and Development, Trützschler GmbH & Co. KG Textilmaschinenfabrik, described their goal as to achieve a constant energy consumption monitoring for every single machine as a self-explanatory feature
Bernd J. Kremer, Technical Director, SETEX Schermuly Textile Computer GmbH, underlined that the modern control systems and software solutions enable active energy management. Kremer gave the implementation of DIN EN 16001 & ISO 50001 as an example to this.
Ulrich Mörschel, Managing Director of Textechno Herbert Stein GmbH & Co. KG, stated that the sophisticated test equipments support the development of energy saving products and creating a low energy consumption. Mörschel gave the products such as fibre-reinforced plastics with special tests for carbon fibres and fabrics as an example.
Matthias Arnold, Vice President Research and Development at Karl Mayer Textilmaschinenfabrik GmbH, Warp Knitting Business Unit stated that the high-quality fibre composites improve the thermal stabilization of the warp knitting elements and reduce energy costs for air conditioning to a considerable extent.