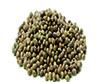
***
In addition to evaluating parameters such as yarn thickness, integrating environmentally friendly fibers, especially innovative materials like hemp, into textile design and production processes is of great importance from a sustainability perspective. This approach is believed to support both the environmental and economic sustainability of the textile industry.
***
Hasan EŞTÜRK, Evren ESKİ, Tamer TAMTÜRK/İntem Triko Sanayi ve Ticaret Anonim Şirketi, Tasarım Merkezi, Akçaburgaz Mahallesi 3097.Sokak No:8 Esenyurt/İstanbul
ABSTRACT
Hemp (Cannabis sativa L.) is an annual plant belonging to the Cannabaceae family, historically used for thousands of years for fiber, food, medicine, ritual, and medical purposes (Li, 1974; Hall & Pacula, 2010).
Some important points to know that make hemp a sustainable raw material are as follows. These;
1. Hemp raw material can be converted into paper 8 times after use.
2. One decare of hemp can produce as much oxygen as 25 decares of trees.
3. While a tree becomes an adult in 20-50 years, hemp grows in 4 months.
4. Pharmaceutical raw materials related to approximately 250 diseases can be produced.
5. Cosmetic materials produced from hemp do not pollute the environment.
6. Hemp can be used in building insulation.
7. Hemp can produce 10 more durable and lighter automotive parts than steel.
8. Hemp contains high amounts of Omega 3-6-9.
9. Clothing made from hemp has better thermal comfort.
10. Biofuel can be obtained from hemp waste.
11. Biopolymers can be produced using hemp.
12. Agriculture can be done without the need for pesticides.
A visual representation of the hemp plant is provided in Figure 1.
Figure 1. Image of the hemp plant (Göre, M., & Kurt, O. (2020).)
All parts of the hemp (Cannabis sativa L.) plant are considered a versatile industrial resource with a wide range of uses. Production can be made from hemp using 5 basic parts of plant. These are listed as seeds, leaves, stems, roots and flowers.
The applications of industrial hemp are illustrated in Figure 2.
Figure 2. Applications of industrial hemp (Gizlenci, Ş., vd. (2019))
The seeds of this plant have been found to be rich in protein, essential fatty acids, and vitamins, making them nutritionally valuable and suitable for use in food products, cosmetic formulations, and biofuel production (Callaway, 2004; Small, 2015; Bouloc, Allegret & Arnaud, 2013). A visual representation of hemp seeds is provided in Figure 3. The oil obtained from the seeds has been used in salad dressings and as a margarine alternative in kitchens, as well as in the production of eco-friendly fuels (Callaway, 2004).
Figure 3. Hemp plant seed (Gizlenci, Ş., vd. (2019))
The fibers obtained from the stems of the hemp plant (shown in Figure 4.a) (shown in Figure 4.b) have been preferred throughout history for textile production due to their durability, breathability, and antibacterial properties, and have also been used in the production of high-quality paper (Ranalli, 2007; Bouloc, Allegret & Arnaud, 2013). The woody parts of the plant have contributed to the sustainable construction sector by being utilized in innovative building materials such as "hempcrete," which are lightweight and have high insulation value (Amaducci et al., 2008). These materials have also been reported to be used as biocomposite raw materials for the automotive industry, as well as bedding for animals and garden mulch material (Ranalli, 2007).
a. Hemp stalk b. Hemp fiber
Figure 4. Hemp stalk and hemp fiber (Gizlenci, Ş., vd. (2019))
The flowers and leaves of the plant (visual provided in Figure 5) have been identified to have significant medical potential due to the cannabinoid and terpene components they contain (Clarke & Merlin, 2013; Small, 2015). Medical cannabis continues to be explored as a supportive treatment option for various health issues such as pain, inflammation, neurological disorders, and anxiety (Small, 2015). Extracts obtained from these parts have also been found to be used in cosmetic product formulations, aromatherapy applications, and essential oil production (Bouloc, Allegret & Arnaud, 2013). The roots have been reported to have some traditional medicinal uses, as well as being considered as an agricultural rotation crop for soil remediation and erosion reduction (Clarke & Merlin, 2013).
Figure 5. Hemp plant flowers and leaves (Gizlenci, Ş., vd. (2019))
The versatility of the hemp plant has been examined with increasing interest in fields such as food, textiles, paper, construction, medicine, cosmetics, and environmental improvement, highlighting its industrial value (Small, 2015). As a result, the potential of hemp has been better understood through research conducted in different regions, making it possible to position it as a resource in line with sustainability goals (Bouloc, Allegret & Arnaud, 2013).
Hemp fiber stands out as an eco-friendly alternative in the textile industry. As a natural resource, hemp is a plant that can be grown with much less water, pesticides, and chemical fertilizers compared to other traditional textile plants. Additionally, due to its rapid growth cycle, hemp can be re-cultivated annually. Hemp fibers possess environmentally friendly properties that decompose biologically faster and are recyclable compared to synthetic fibers. The production of hemp textile products consumes less energy and water, while the use of organic hemp helps improve soil health. Consequently, the environmental impacts of hemp textile products are significantly lower when compared to other textile materials, making them an essential part of the sustainable fashion industry (Scaglia, 2019; Matos, 2020).
Within the scope of this study, to achieve sustainability in textiles, obtain a more environmentally friendly textile product, and investigate the usability of the obtained product, flat knitted fabrics containing 80% tencel and 20% hemp in Ne 10 yarn count, and 80% recycled polyester and 20% hemp in Ne 12 and Ne 18 yarn counts were produced. Shrinkage and pilling tests were then applied to the obtained knitted fabrics, and their performances were evaluated.
İNTEM KNITWEAR AND SUSTAINABILITY VISION
The title "Green Harvest For the Future" reflects İntem Knitwear's perspective, principle, and vision on sustainability. This approach stems from the project name we have given to our renewable energy sources production facility. Our Energy Management unit regularly monitors emissions from energy and natural gas consumption and prepares carbon reduction projects (CRP) to address the world we have borrowed from future generations. By building the future today, we track carbon emissions per product and kilogram, and meet all our energy needs from our Solar Power Plant, reducing our carbon footprint. Knowing that only 0.3% of the world's water is usable, we monitor our water footprint daily and work diligently towards our reduction targets.
I would like to express our hope to be a "nail" in the industry with the following words:
"A nail saves a shoe, a shoe saves a horse, a horse saves a commander, a commander saves an army, and an army saves a country."
Tamer TAMTÜRK
In the field of environmental sustainability, we have set intermediate and final targets for reducing emissions and water footprint, and have created our prioritization matrix within the framework of the Sustainable Development Goals. In our work on product life cycle, we meticulously conduct product cycle analyses based on the business management approach. This way, we take the necessary steps to monitor and improve all processes from "cradle to grave." Additionally, I would like to emphasize that at İntem Knitwear, we not only focus on producing the final product but also that the majority of our team consists of women. I would like to conclude my writing with a quote from the famous fashion designer Anne Klein:
"Clothes won't change the world, the women who wear them will."
Evren ESKİ
İntem Knitwear's sustainability projects encompass multi-dimensional approaches such as the preference for eco-friendly raw materials, optimization of production processes, enhancement of energy and water efficiency, waste minimization, social responsibility initiatives, and compliance with international sustainability standards. Within this scope, İntem Knitwear, as part of the activities of the Design and R&D Center, undertakes projects in various areas including the use of recycled raw materials, materials that reduce energy and water consumption, and the development of designs from the company's own waste.
1. INTRODUCTION
Sustainability in the textile sector refers to the balanced management of environmental, economic, and social dimensions. This concept aims to efficiently use natural resources, reduce waste, and lower the carbon footprint at all stages from production processes to the use of final products. It also includes social responsibility elements such as respect for workers' rights, safe working conditions, and contributions to the community. The adoption of innovative technologies and circular economy practices plays a key role in ensuring sustainability in the sector. For example, the use of recycled raw materials and production techniques that reduce water and chemical use minimize the environmental impact of the textile industry. Thus, sustainability aims not only to provide environmental benefits but also to support long-term economic growth and social welfare (Şen, 2008; Fletcher, 2014).
Sustainable fibers in the textile industry are of great importance for reducing environmental impacts and efficiently using resources. Materials such as organic cotton, bamboo, hemp, lyocell (Tencel), recycled polyester, and wood-based fibers stand out as prominent options in sustainable textile production. These fibers provide environmental benefits with features such as lower water and energy consumption during production processes, reduced carbon emissions, and decreased chemical use. Especially fibers like hemp and lyocell are biodegradable and derived from renewable sources, making them suitable for circular economy principles. At the same time, materials like recycled polyester support environmentally conscious production methods by reducing the amount of waste. The use of sustainable fibers not only ensures the production of eco-friendly textile products but also steers the industry towards a more responsible future (Shen et al., 2010; Kozlowski and Mackiewicz-Talarczyk, 2012; Fletcher, 2014).
Hemp fiber has many superior qualities in terms of environmental, economic, and performance aspects among sustainable textile fibers. The hemp plant requires minimal water and fertilizer during cultivation and can often be grown without pesticides, significantly reducing its environmental impacts compared to organic cotton. The stages of obtaining yarn from hemp fiber are shown in Figure 6. Compared to fast-renewable fibers like bamboo, hemp requires fewer chemical processes during processing, thus causing less environmental harm. Unlike recycled polyester, hemp is a fully biodegradable fiber, offering advantages in waste management. Compared to cellulose-based fibers like lyocell (Tencel), hemp has a higher carbon absorption capacity and also helps prevent soil erosion. Additionally, hemp fibers are an ideal choice for long-lasting and healthy textile products due to their durability and natural breathability. These features make hemp fiber an unrivaled alternative in sustainable textile production (van der Werf, 2004; Ranalli and Venturi, 2004; Cherrett et al., 2005; Kozlowski and Mackiewicz-Talarczyk, 2012).
Figure 6. Stages of yarn production from hemp fiber (Rehman, M., vd. (2021))
In this study, the advantages of hemp fibers over other sustainable fibers were discussed, and the effects of a 20% hemp fiber blend on pilling and shrinkage in knitted fabrics were examined.
2. AN EXAMPLE FOR THE USE OF HEMP FIBER IN KNITWEAR
In this study, yarns with a composition of 80% Tencel and 20% hemp in Ne 10 yarn count, and 80% recycled polyester and 20% hemp in Ne 12 and Ne 18 yarn counts were sourced from Karacasu Textiles. The test results for the yarns are provided in Table 1.
Table 1. Test Results of the Yarns
Yarn Count |
RKM |
RKM |
%U |
%CVm |
NEPS |
% Elongation |
Ne 10 |
23,32 |
1,81 |
11,94 |
15,49 |
11,3 |
11,59 |
Ne 12 |
26,63 |
2,41 |
18,07 |
23,59 |
4,18 |
13,6 |
Ne 18 |
26,19 |
6,14 |
20,48 |
27,32 |
6,55 |
12,43 |
In this study, plain knitted fabrics with a weight of 231 g/m², 360 g/m², and 292 g/m² were produced from different yarn counts.
The codings for the obtained samples are provided in Table 2
Table 2. Fabrics used in the study
Codes |
Yarn Count |
Knit Type |
K 1 |
Ne 10 |
Plain Knit - Knitwear |
K 2 |
Ne 12 |
Plain Knit - Knitwear |
K 3 |
Ne 18 |
Plain Knit - Knitwear |
To examine the performance of the obtained knitted fabrics, ISO 12945-1:2001, ISO 6330, and ISO 5077 tests were conducted.
3. RESULTS
The pilling results obtained in the study are provided in Table 2.
Table 2. Pilling test results for the samples.
Samples |
Pilling Results |
K 1 |
4/5 |
K 2 |
4 |
K 3 |
|
When Table 2 is examined, it can be seen that the pilling rating of fabric 1, with a lower yarn count, is 4/5, which is half a point better than the pilling ratings of fabrics 2 and 3. As is known, yarn thickness directly affects pilling formation in knitted fabrics. Fabrics made from finer yarns may have a tighter surface structure, which reduces the likelihood of fibers rising to the surface and entangling to form pills. On the other hand, thicker yarns can create looser structures, facilitating the movement of fibers to the surface and increasing the tendency for pilling (Hsieh and Miller, 1992; Hearle, 2001; Basal and Oxenham, 2006; Oğlakçıoğlu and Marmaralı, 2007; Ute and Schorsch, 2010).
The washing shrinkage test results for the samples are provided in Table 3.
Table 3. Shrinkage test results for the samples.
Samples |
Shrinkage width (%) |
Shrinkage length (%) |
K 1 |
-2 |
0 |
K 2 |
-2 |
3 |
K 3 |
-2 |
2 |
When the shrinkage results obtained in Table 3 are examined, it is observed that the shrinkage rates are similar to each other and fall within the range of 2-3%. Therefore, it can be concluded that the yarn thickness does not have a significant effect on the shrinkage values of the samples. This is because the effect of yarn thickness on shrinkage is also related to other factors such as the type of fiber used, yarn twist ratio, knitting density, and finishing processes.
The twist stability results for the samples are provided in Table 4.
Table 4. Twist stability of the samples.
Samples |
Rotation Stability (%) |
K 1 |
4 |
K 2 |
4 |
K 3 |
3 |
When the results obtained in Table 4 are examined, it is observed that the twist percentage of fabrics 1 and 2 was measured as 4%, while the twist percentage of fabric 3 was measured as 3%. Accordingly, it can be said that the twist stability of fabric 3, made from thicker yarns, is better. This can be briefly explained as follows: In plain knitted fabrics, yarn thickness significantly affects twist stability. Yarn thickness is a critical factor that determines the physical properties and structural stability of the fabric. Fine yarns have a more sensitive structure in terms of flexibility and deformation, and therefore can negatively affect twist stability. This situation is related to the lower strength and elasticity differences of fine yarns. Fabrics made from thicker yarns are generally more stable and resistant to twists because these yarns provide greater mechanical durability to the fabric structure (Spencer, 2001; Ute, 2010, Çelik and Gürarda, 2011; Havelka and Čarnogurská, 2015; Mikučionienė and Baltušnikaitė, 2017).
4. GENERAL EVALUATION
The industrial hemp (cannabis sativa) is a versatile plant with a wide range of uses in textile, construction, food, energy, pharmaceutical and other industries. This species, which has low psychoactive effects, is generally distinguished by its tetrahydrocannabinol (THC) content below 0.3%. The cultivation of industrial hemp is controlled by legal regulations in many countries. In Turkey, industrial hemp production can be done legally in 20 cities under certain conditions. However, government permission is required for production and the THC content is strictly regulated. Hemp fabric has become an important part of the eco-friendly fashion and sustainable textile movement. Important textile brands and small-scale manufacturers are discovering the potential of hemp and developing innovative products in this field.
In this study, the effects of yarn thickness on fabric properties in plain knitted fabrics have been examined in detail. Thus, it is aimed to integrate hemp fiber products into the design and production processes of İntem Triko.
The results show that yarn thickness directly affects pilling formation and twist stability, but does not create a significant difference in shrinkage values. Fabrics made from fine yarns have a tighter surface structure, reducing pilling tendency and providing better pilling performance in such fabrics. On the other hand, fabrics made from thicker yarns have increased mechanical durability, which enhances twist stability and reduces the likelihood of deformation in these fabrics. In the shrinkage results, it was observed that yarn thickness alone is not a parameter that determines the shrinkage performance of plain knitted fabrics.
Additionally, it should be emphasized that the use of hemp fiber, in line with sustainability goals, is an important alternative for the textile industry. In addition to evaluating parameters such as yarn thickness, integrating environmentally friendly fibers, especially innovative materials like hemp, into textile design and production processes is of great importance from a sustainability perspective. This approach is believed to support both the environmental and economic sustainability of the textile industry.
REFERENCES
-Amaducci, S., Zatta, A., Raffanini, M., ve Venturi, G. (2015). Characterization of hemp (Cannabis sativa L.) genotypes for pulp and paper production. Industrial Crops and Products, 68, 29-37.
-Basal, G., & Oxenham, W. (2006). Effect of fiber properties on pilling performance of knitted fabrics. Textile Research Journal, 76(9), 673–681.
https://doi.org/10.1177/0040517506065842
-Bouloc, P., Allegret, S., & Arnaud, L. (Eds.). (2013). Hemp: Industrial Production and Uses. CABI Publishing.
-Callaway, J. C. (2004). Hempseed as a nutritional resource: An overview. Euphytica, 140(1–2), 65–72.
-Carus, M., Karst, S., Kauffmann, A., Hobson, J., & Bertucelli, S. (2013). The European Hemp Industry: Cultivation, processing and applications for fibres, shivs and seeds. European Industrial Hemp Association (EIHA).
-Cherrett, N., Barrett, J., Clemett, A., Chadwick, M., & Chadwick, M. (2005). Ecological footprint and water analysis of cotton, hemp and polyester. Stockholm Environment Institute. Retrieved from https://www.sei.org
-Clarke, R. C., & Merlin, M. D. (2013). Cannabis: Evolution and Ethnobotany. University of California Press.
-Çelik, P., & Gürarda, A. (2011). Effects of yarn properties on the fabric performance of single jersey knitted fabrics. Industria Textila, 62(2), 75-81.
-Fletcher, K. (2014). Sustainable fashion and textiles: Design journeys. Routledge.
-Göre, M., & Kurt, O. (2020). Bitkisel üretimde yeni bir trend: Kenevir. International Journal of Life Sciences and Biotechnology, 4(1), 138-157.
-Havelka, A., & Čarnogurská, M. (2015). Influence of yarn parameters on knitted fabric properties. Journal of Textile and Apparel, Technology and Management, 9(2), 1-10. Retrieved from https://textilemanagementjournal.org
-Hearle, J. W. S. (2001). Physical properties of textile fibers (4th ed.). Woodhead Publishing.
-Hsieh, Y. L., & Miller, A. (1992). Pilling propensity and related fabric properties of spun yarns. Textile Research Journal, 62(8), 483–490.
https://doi.org/10.1177/004051759206200807
-Kozlowski, R., & Mackiewicz-Talarczyk, M. (2012). Hemp fibre–a natural resource for diverse applications in textiles. Textile Research Journal, 82(12), 1231–1240. https://doi.org/10.1177/0040517512446063
-Li, H. L. (1974). An archaeological and historical account of cannabis in China. Economic Botany, 28(4), 437-448.
-Matos, F. (2020). *Hemp for Sustainable Textiles*. Journal of Textile Science, 25(3), 123-137.
-Mikučionienė, D., & Baltušnikaitė, J. (2017). Structural and mechanical properties of knitted fabrics. Fibres & Textiles in Eastern Europe, 25(5), 40-47.
https://doi.org/10.5604/12303666.1221745
-Oğlakçıoğlu, N., & Marmaralı, A. (2007). Effects of yarn properties on pilling performance of knitted fabrics. Textile Research Journal, 77(3), 191–196.
https://doi.org/10.1177/0040517507071570
-Ranalli, P. (2007). Hemp: Industrial Production and Uses. Nova Science Publishers.
-Ranalli, P., & Venturi, G. (2004). Hemp as a raw material for industrial applications. Euphytica, 140(1–2), 1–6.
https://doi.org/10.1007/s10681-004-4749-8
-Rehman, M., Fahad, S., Du, G., Cheng, X., Yang, Y., Tang, K., ... & Deng, G. (2021). Evaluation of hemp (Cannabis sativa L.) as an industrial crop: a review. Environmental Science and Pollution Research, 28(38), 52832-52843.
-Roulac, J. W. (1997). Hemp Horizons: The Comeback of the World’s Most Promising Plant. Chelsea Green Publishing.
-Shen, L., Worrell, E., & Patel, M. K. (2010). Environmental impact assessment of man-made cellulose fibers. Resources, Conservation and Recycling, 55(2), 260–274. https://doi.org/10.1016/j.resconrec.2010.10.001
-Small, E. (2015). Cannabis: A Complete Guide. CRC Press.
-Spencer, D. J. (2001). Knitting technology: A comprehensive handbook and practical guide. Woodhead Publishing.
-Şen, A. (2008). Sustainable textiles: Life cycle and environmental impact. Woodhead Publishing.
-Scaglia, B. (2019). *Sustainable Textiles: Environmental Impacts and Solutions*. Springer.
-Ute, B. (2010). Yarn twist and its effect on fabric properties: A study on knitwear. Textile Research Journal, 80(13), 1273-1280.
https://doi.org/10.1177/0040517510361793
-Ute, J., & Schorsch, T. (2010). Influence of yarn fineness and surface structure on pilling in knitted fabrics. Fibers and Polymers, 11(5), 758–765.
https://doi.org/10.1007/s12221-010-0758-6
-Van der Werf, H. M. G. (2004). Life cycle analysis of field-grown hemp and its products. Industrial Crops and Products, 19(2), 193–204.
https://doi.org/10.1016/j.indcrop.2003.10.010
-https://arastirma.tarimorman.gov.tr/ktae/belgeler/kenevir_tarimi_kitabi.pdf
RKM
RKM
%CV
%U
%CVm
NEPS
%200
% Elongation
Ne 10
23,32
1,81
11,94
15,49
11,3
11,59
Ne 12
26,63
2,41
18,07
23,59
4,18
13,6
Ne 18
26,19
6,14
20,48
27,32
6,55
12,43
[endif]
Yarn Count |
RKM |
RKM |
%U |
%CVm |
NEPS |
% Elongation |
Ne 10 |
23,32 |
1,81 |
11,94 |
15,49 |
11,3 |
11,59 |
Ne 12 |
26,63 |
2,41 |
18,07 |
23,59 |
4,18 |
13,6 |
Ne 18 |
26,19 |
6,14 |
20,48 |
27,32 |
6,55 |
12,43 |